Printed in the January/February 2020 issue of Ethanol Today published by the American Coalition for Ethanol
Ethanol producers that added the milling and separation technologies developed in the past decade are realizing multiple process improvements alongside diversified feed products. This year, ICM Inc. rolled out its new Feed Optimization Technology to add one more feed option to its suite of offerings.
In the ICM approach, the new technologies have been stacked, starting with Selective Milling Technology (SMT) / Selective Milling Technology version 2 (SMT V2) that aims to right-size the corn profile to enhance downstream solid and liquid separation. SMT/SMT V2 also exposes more starch for fermentation and increases the amount of oil for recovery.
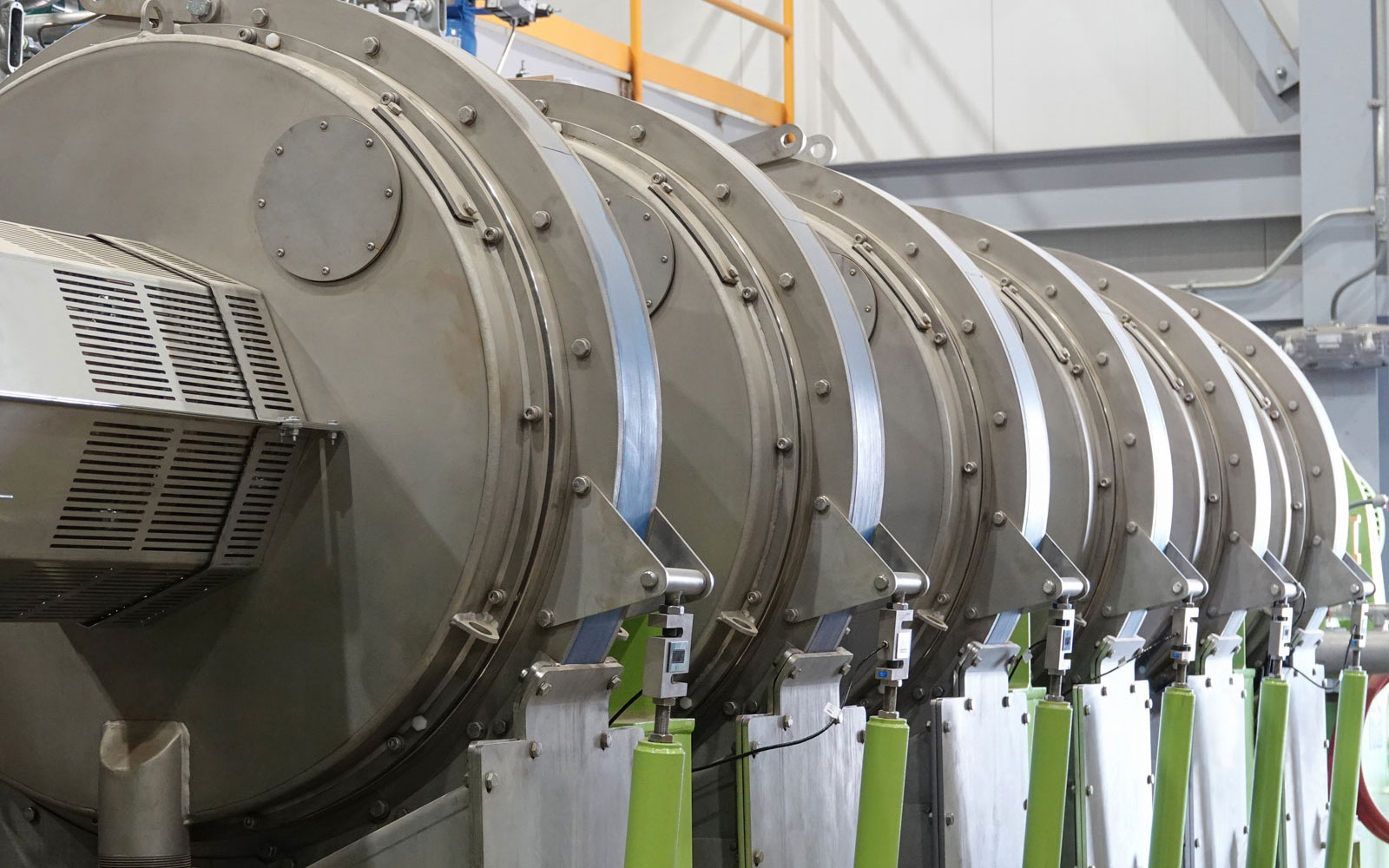
FST Press: ICM’s Fiber Separation Technology removes fiber, which frees up fermentation capacity and enhances overall plant efficiency.
Fiber Separation Technology (FST) / Fiber Separation Technology Next Gen (FST Next Gen) can be added after SMT/SMT V2 to wash away the starch, oil and proteins, leaving the fiber behind. “The fiber bypasses the ethanol process, while advancing the more valuable components for further processing downstream,” explains Chuck Gallop, Operations Development Manager for ICM Technology Development. “Removing the fiber also means the downstream processes can become more efficient.”
FST Next Gen removes fiber, which frees up fermentation capacity and enhances overall plant energy efficiency. After distillation, the suite of technologies optimizes the remaining separations. “What are left after removing the ethanol are fat and protein, some fine fiber and water,” Gallop says.
Traditionally, the decanters were the only technology used to separate the whole stillage into wet cake heading to the dryers and thin stillage bound for the evaporators. ICM’s Thin Stillage Solids Separation System (TS4) and Feed Optimization Technology (FOT) offer new options.
With patent-pending TS4, suspended solids are removed from the thin stillage, leaving just the solubles to be concentrated in the evaporators. The newest patent-pending technology, FOT adds processing steps to further concentrate the separated protein solids into a 53+ percent yeast-rich, protein feed.
The technologies can be installed individually and stacked, Gallop says. Dozens of plants have installed SMT, 11 have added FST, Five plants now have TS4 and the first commercial installation of FOT is underway. The company is also rolling out a new acronym and name for the integrated technologies trademarked APP, for Advanced Processing Package.
The operational benefits in the 11 plants that have installed Fiber Separation Technology have been significant. “We see up to 14 percent increase in ethanol capacity,” Gallop says. “It means you can run more corn through your existing plant without additional fermenters, which means more revenue from your fixed overhead.”
There are roughly 4 pounds of fiber in a bushel of corn removed before fermentation with FST, Gallop says. “This means 4 pounds of fiber will bypass these ethanol process—fermentation, distillation, centrifugation—and will go right to the dryer. We do that because there’s no beneficial value to the rest of the plant for that fiber to go through it.”
Besides added capacity, removing fiber also results in energy savings. “Depending on the plant and how it’s running, we can see in excess of 3,000 Btu per gallon of ethanol produced in energy savings,” Gallop says. “Any time there’s a temperature adjustment, dollars are spent to heat up the fiber or cool it down. Any time there is physical movement from point A to B, electricity dollars are spent to pump it. Removing the fiber avoids that waste.” Removing fiber has also resulted in lower chemical costs for cleaning and pH adjustments, he adds.
By pulling the fiber out early in the process, every downstream process and piece of equipment can be optimized, Gallop says. “As an example, if that fiber stays in the whole stillage, a typical decanter centrifuge achieves somewhere between 37 and 39 percent solids in the wet cake. With FST, because we employ a proprietary rotary press to dewater the fiber, we’re able to achieve 43 to 45 percent solids. We’re talking 5 moisture points, all the while using roughly one-tenth the connected horsepower to do the same work.”
TS4 treats the liquid portion of the decanter separation, with its own positive operational impacts. “By pulling out the suspended solids, we are now truly making just condensed solubles syrup,” Gallop says. “The volume of syrup to the dryer is reduced. And, when we decrease the concentration of total suspended solids, we reduce syrup viscosity, which means the evaporator recirculating pump becomes exponentially more efficient.” The net result of the increased efficiency is more pounds of water evaporated per unit of energy, plus reduced fouling.
TS4 Sedicanters: ICM’s patent-pending Thin Stillage Solids Separation System removes suspended solids from the thin stillage, leaving just the solubles to be concentrated in the evaporators.
The newest technology, FOT, is less about operational enhancement, although increased oil recovery yields are expected, and more about providing an additional feed option. Plants implementing FST can add the fiber removed at the front end back onto the wet cake at the back end to be sold as typical distillers grains. A second option is to add syrup to the fiber, creating a new ruminant feed that has performed well in cattle feed trials. The remaining low-fiber distillers grains is now higher in protein at around 40 percent. Adding the new FOT option treats the yeast-rich distillers grains to achieve a consistent 53 percent protein product that ICM has trademarked as PROTOMAX. Gallop adds the split among feed options can be easily adjusted.
The goal has been to create a suite of technologies that offer ethanol producers flexibility, Gallop says. “We’re trying to give ethanol producers the tools for their toolbox to be successful. As a technology provider, the last thing we want to do is provide a hammer and say this is going to fix all your problems. The hammer very well could be the best tool for a mason, but for a watchmaker, it wouldn’t come close. We want to load up the tool box with the tools necessary for plants to be successful, with flexibility depending on input costs and the needs of local, national or international feed markets.” He adds that the ICM team that has worked on the technology suite is really proud of the development. “The attractive part of the flexibility of this technology is that you can process as much of the flow as you want and produce the feed products the market desires.”
The newest technology, FOT, and the integrated suite, APP, aligns with ICM’s vision of bringing efficient technologies to the market, offering flexibility while reducing energy and operational costs, Gallop says.